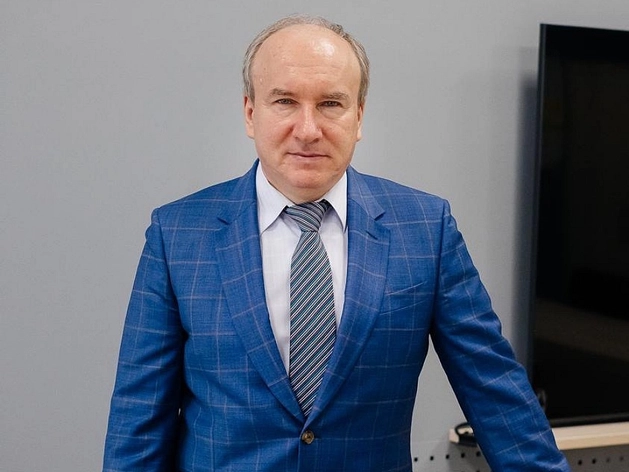
В этом году челябинская группа «ЭлМетро» реализует инвестиционный проект на 105 млн рублей, который позволит выпускать измерительные приборы для труб большого диаметра.
Такое оборудование особенно востребовано в нефтегазовом секторе. В интервью «Деловому кварталу» Александр Жестков рассказал о проекте и его значении для российского машиностроения.
В марте мы публиковали новость о том, что Фонд развития промышленности выдал «ЭлМетро» заем на 50 млн рублей. Расскажите, что планирует реализовать компания, куда собираетесь потратить деньги?
— Основное направление нашей компании — разработка и производство кориолисовых расходомеров. Это самый точный тип измерения расхода жидкостей и газов в трубопроводах. В этом сегменте наша компания занимает лидирующие позиции по объему выпускаемой в РФ продукции.
Наиболее востребована наша продукция в нефтегазовом секторе, причем мы отмечаем повышенный интерес нефтяных компаний к измерительным устройствам большого диаметра. Поэтому приняли стратегическое решение развивать свои производственные мощности в направлении выпуска приборов больших типоразмеров.
Для этого требуется специальное оборудование, прежде всего высокотемпературная крупноразмерная вакуумная печь. Это сложное, высокотехнологичное и дорогостоящее оборудование, для приобретения которого мы получили льготное кредитование от Фонда развития промышленности.
Когда планируете запустить новое оборудование для производства приборов большого диаметра?
— Печь в процессе изготовления. Специально для нее мы построили отдельное двухэтажное здание, высота печи — 14 метров. Рассчитываем получить оборудование к концу лета, после монтажа начнется пусконаладка, которая займет минимум 2 месяца.
Расходомеры какого диаметра вы планируете производить на новом оборудовании?
— Эту печь мы рассчитывали на типоразмеры до условного диаметра 250 мм и пропускной способностью 1500 м3 жидкости в час.
Как скоро рынку ждать новые приборы?
— Освоение новых направлений — длительный процесс. Около года у нас уйдет на то, чтобы наладить потоковое производство расходомеров нового диаметра. Но в этой печи мы также планируем производить и имеющиеся модели приборов. Благодаря новому оборудованию мы повысим производительность и снизим риски простоя производства.
Какое еще оборудование вам понадобится, помимо высокотемпературной печи?
— Кроме печи, мы закупили новые проливочные установки и роботизированный комплекс сварки. Плюс сейчас стараемся максимально автоматизировать любую операцию и делать так, чтобы сотрудник работал не на универсальном, а специальном оборудовании.
Например, у нас есть климатические камеры, через которые проходят все наши приборы. Они создают специальные условия — влажность, высокую и низкую температуру, — чтобы проверить, как будет работать датчик в реальных условиях. Такая проверка позволяет резко уменьшить количество брака в производстве и улучшить метрологические характеристики наших приборов. Насколько я знаю, подобная операция в цикле производства у отечественных конкурентов отсутствует.
Новое оборудование будем запускать на площадях, которые приобрели в прошлом году и сейчас реконструируем.
Расскажите подробнее о переезде. В прошлом интервью вы упоминали, что выкупили у завода «Прибор» корпус на 9000 кв. м на Комсомольском проспекте. Наверняка не так просто перенести производство?
— Вы правы, перенос производства — непростой процесс. Переоборудование новых площадей и организация цеха уже сравнялись с затратами на покупку здания, к тому же у нас не просто переезд, а перестройка технологических цепочек. Мы хотим организовать потоковое производство с более высокой производительностью и возможностью лучше контролировать процессы и качество приборов.
За последний год выручка компании выросла в два раза и превысила 2 млрд рублей. Вы вкладываете ресурсы в расширение производства, в сотрудников. Стало ли при этом сложнее управлять процессами? С какими трудностями столкнулись при росте?
— Чтобы справиться с задачами, мы запустили несколько новых проектов организационного плана. В первую очередь внедрили систему управления производством на базе отечественного ПО. Проектом занимается отдельная команда, которая последовательно внедряет систему в работу подразделений, начиная со склада и заканчивая планированием производства.
У сотрудников нет сопротивления? Обычно при внедрении новых систем работники могут не захотеть уходить от привычных процессов.
— Нет, наоборот, все уже заждались. Всем понятно, что это резко облегчит работу. Управлять предприятием нужно системно и с помощью технологий.
С ростом выручки растет и количество сотрудников. Одно дело, когда управляешь коллективом в 50 человек, и совсем другое, когда в команде — почти 300. Как изменился подход к управлению командой за это время?
— Наша группа компаний привлекла консалтинговое агентство, которое помогает преобразовать структуру предприятия и четко обозначить конечный ценный продукт для каждого человека и для каждого подразделения. Мы планируем внедрить метрики и отслеживать их, чтобы каждому сотруднику было понятно, чего от него ждет компания, как оценивает его работу, какие есть перспективы роста.
У вас будет напряженный год: и запуск нового оборудования, и переезд, и внедрение новой системы управления предприятием. На чём еще планируете сосредоточиться в 2024 г.?
— У нас принят план НИОКР, проще говоря, план разработок новых приборов. Мы концентрируемся на прорывных проектах, хотим обеспечить максимальный охват в линейке ультразвуковых и кориолисовых расходомеров, расширить линейку микроволновых радиочастотных уровнемеров. Параллельно совершенствуем существующие приборы. В прошлом году изучили потребности наших заказчиков — нефтяников, газовиков, энергетиков, химической и пищевой промышленности. Сейчас работаем над их запросами.
Получается, что со стороны рынка есть колоссальный спрос на отечественные расходомеры, который нужно удовлетворить.
— Тут два варианта: либо их удовлетворит отечественный производитель, либо наши партнеры из Китая.
Поэтому вы так активно действуете сейчас — ставка на то, чтобы успеть занять освободившиеся после ухода иностранных компаний ниши?
— Да, и мы позиционируем себя именно как отечественное производство. Основные части в приборе — конструкция, схемотехника, программное обеспечение — должны быть российскими, чтобы мы полностью управляли прибором. А те, кто занимается псевдоимпортозамещением, то есть ребрендингом китайских товаров, не могут этого достичь.
Как вы оцениваете развитие российского машиностроения? В каком направлении движется отрасль?
— Сейчас активно развивается направление интеллектуальных датчиков. Термин для отрасли неновый, но сейчас в него вкладываются другие смыслы. Сегодня интеллектуальный датчик — это прибор с системой глубокой самодиагностики. Он сам себя тестирует и проверяет. Это важно для заказчиков, у которых приборы стоят в труднодоступных местах и иногда участвуют в таких процессах, которые нельзя останавливать. То есть снять прибор и проверить его работу просто невозможно. Поэтому мы первыми в России ввели имитационную поверку без снятия расходомера и даже без остановки процесса.
Неприятная особенность текущего момента — нехватка специалистов. Это давно стало общей темой на встречах с коллегами.
Мы стараемся привлечь интересными задачами, высокими зарплатами, хорошей атмосферой в коллективе. Также намерены больше работать с вузами. В планах — встречи с руководством ЮУрГУ и ЧелГУ, ведущими университетами нашего города. Рассчитываем на то, чтобы специалистов нашего профиля можно было готовить в целевых группах.
Беседовала Наталья Горюнова
Реклама
Erid: LjN8KZJhC
ООО «ЭлМетро-Инжиниринг»,
ИНН 7448109853
Еlmetro.ru.